Technology &
Failure Analysis Lab
Passive and active electronic components, from resistor to complex System-in-a-package devices.
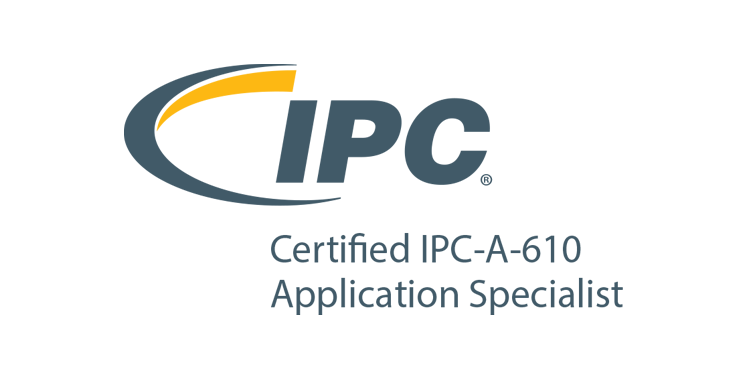
IPC-A-610 Certified Laboratory
Destructive Physical Analysis & Construction Analysis
DPA & CA
Physical and chemical control of the device quality.
The analysis flow is defined by the package type and reliability level requirements.
- External visual inspection
- X-Ray 2D-Radiography or 3D-Tomography
- Hermetic seal testing (fine and gross leak)
- EDS (Energy Dispersive Analysis) and XRF (X-Ray Fluorescence) material analyses
- Acoustic microscopy
- Particle Impact Noise Detection (P.I.N.D.) testing
- Solderability (Wetting Balance)
- Residual Gas Analysis/internal water-vapor content (RGA)
- Delid/decap/case removal (Wet, Dry, Mechanical)
- Internal visual inspection
- Bond strength
- Die shear
- SEM (Scanning Electronic Microscope) / EDS inspection
- Layer deprocessing
- Micro-sectioning (Mechanical, FIB or Ion Milling)
Reverse
Construction Analysis
RCA
Light or deep dive physical analysis for die and assembly process characterization.
The analysis flow is proposed for a quick technology analysis or deep dive sub process identification.
- DPA and CA flow
- Specific flow or specific feature
- Layout analysis
- Die level material analysis and dimension analysis
- FIB (Focus Ion Beam) or TEM (Transmission Electron Microscopy) cross section with chemical analysis of layers
- SIMS (Secondary Ion Mass Spectrometry), Tof SIMS (Time-of-Flight SIMS), AFM (Atomic Force Microscope), XPS (X-Ray Photoelectron Spectroscopy)
Failure Analysis
FA
To try to identify root cause of the failure mode and mechanism
- Electrical fail confirmation (digital to power 0 to 3 kV)
- Radiographic X-Ray 2D or 3D Tomography
- Delid/decap/case removal (Wet, Dry, Mechanical)
- Acoustic microscopy
- Backside preparation capability
- Defect location Lock-in-Thermography
- Defect location Light emission
- Defect location OBIRCH (Optical Beam Induced Resistance Change)
- MICRO-probing (up to +200°C)
- Passive voltage contrast
- Die level material and dimension analysis
- FIB or TEM cross section with chemical analysis of defect
- Application support
Printed Circuit Board Control
PCB Assembly control
Monitoring and control of PCB/PCBA process following IPC, MIL, IEC, ECSS, and JEDEC.
- External visual inspection
- Cross sectioning
- Optical visual examination
- Stand-off Thickness measurement
- SEM/EDS examination and measurement
- Radiographic X-Ray2D or 3D Tomography
- Real Time Resut Sharing (virtual lab)
Sample preparation
Sample preparation
For physical analysis, defect location, FIB (Focus Ion Beam) circuit edit, radiation and laser tests.
- Package opening for die access with Gold, Silver, Copper wires and clip (Chemical, Microwave Induced Plasma, Mechanical)
- Die extraction
- Die re-assembly on PCB
- Re-bonding with gold wire
- Backside thinning and mirror polishing
- Die Block Schielding
- Backside thinking and mirror polishing down to 10µm si lift